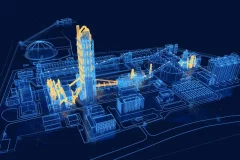
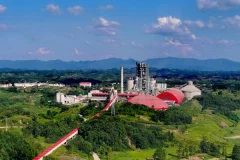
In the quest for sustainability and reduced environmental impact in cement production, Alternative Fuel and Raw Materials (AFR) play a pivotal role. AFR refers to the use of non-conventional materials as a substitute for traditional fuels and raw materials in cement manufacturing. These materials typically include various types of waste, such as industrial by-products, biomass, or non-recyclable materials, which would otherwise end up in landfills. The integration of AFR in cement kilns not only helps in managing waste effectively but also significantly reduces the reliance on fossil fuels, leading to lower carbon emissions. The utilization of AFR is a complex process, involving careful sourcing, processing, and compatibility assessment with existing cement production technology, all aimed at maintaining the quality of the cement while ensuring environmental compliance.Fuel may vary from Liquid, Semi solid or Solid from Biomass, Paint sludge, MSW, Tyre chips,Pharmaceutical wastes etc. which are having
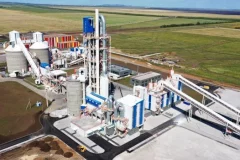
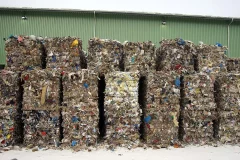
Cement Plant Refuse Derived Fuel System
2024-01-03The cement industry is undergoing a positive and remarkable transformation: replacing fossil fuels with refuse derived fuels (RDF), solid recover fuels (SRF) or biomass. This measure helps to reduce carbon emissions, achieve more environmentally friendly cement production processes, and fulfill the commitment of cement enterprises to sustainable development.GEP ECOTECH is committed to promoting sustainable development in the cement industry, and we offer a variety of innovative alternative fuel solutions for this purpose. Our solutions cover various kinds of materials and feeding requirements, tailoring the best solutions for customers to ensure stable and high-quality fuel supply.Shredding SystemA powerful shredding system is the key to the successful production of high-quality RDF/SRF. GEP ECOTECH's multi-stage shredding system doesn't fear the challenges of complex materials. From pre shredder to shearing shredder, and the eye-catching single shaft shredder, our shredders' durability and trouble free
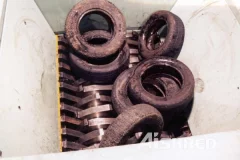
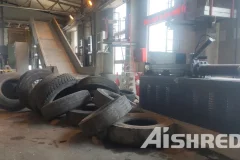
Waste Tyre Shredding Machine for Sale
2022-04-24The GDT series tire shredder is a unique tire crushing machine designed specifically for recycling tires from trucks, agricultural and special equipment, aircraft and car wheels. The shredder has a built-in grate that allows you to calibrate the output material (rubber chips) by size.Distinctive features of the tire shredding machine from GEP ECOTECH are compactness, power, as well as an integrated unloading system with the ability to adjust the size of the outgoing fraction using grates.Productivity Capacity - up to 30 tons per hour.The Tire Shredder GDT series can use a hydraulic drive. Such a drive is necessary for tearing a metal cord (metal cord), which is made from a very elastic and hard metal.LOW MAINTENANCE COSTSGEP ECOTECH has developed a new tire shredder concept with a double rotor and low maintenance costs. The cutting blades are made of high quality wear resistant steel. The design of the rotor and blades allows very fast replacement during maintenance. The cost of knives is quite low due to
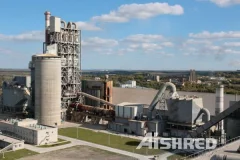
Co-processing Waste in Cement Industry
2022-04-21The problem of waste is one of the most urgent on the world agenda, According to the World Bank, the world generates 2.01 billion tonnes of waste every year, with at least 33 percent of that—extremely conservatively—not managed in an environmentally safe manner. Therefore, the most important task is to clear the waste and create a system that will allow separating waste, competently managing its flows, processing it and without harm to nature. Turning the so-called “tailings” into cement, which remain at the waste sorting complexes after the extraction of all useful recyclable materials, is one of the most environmentally friendly and effective solutions to this problem. The use of alternative fuels from municipal solid waste (MSW) in cement production will help global achieve environmental goals.Waste Disposal in the Production of CementLimestone, clay and thermal energy are needed to make cement. The cost of the latter is 30% of all production costs. The cement industry uses a variety of fossil fuels to
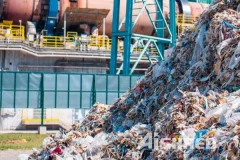
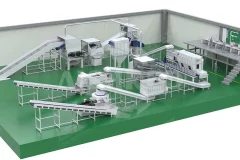
Due to the continuing energy cost fluctuations and the discussions on the sustainable protection of resources the cement industry has hardly enabled to reduce its entire energy and power demand as a result of technical optimisation of its cement production. With the rising energy prices, people have successively used petroleum and coal as the main fuel for cement production. Later, people began to explore the use of waste oil and tires. Nowadays, as people pay more and more attention to reducing carbon emissions, the waste-to-fuel technology has become more and more mature, and many cement kilns have begun to use municipal solid waste or industrial and commercial waste as alternative fuels.Substituting Coal and Petcoke with Alternative fuelsCoal and petcoke, two of the most carbon-intensive fuels, are typically used to heat cement kilns. The substituting coal with lower-carbon fuels offers the greatest short-term potential to reduce CO2 emissions in the industry. Most alternative fuels have a lower carbon
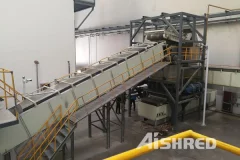

Industrial Shredder for Cement Industry
2022-04-06Cement production is an extremely energy-intensive process that emits approx. 8% of the world’s CO2. There are huge economic and environmental benefits to be made by replacing fossil fuels with alternative fuels made from waste. Cement producers utilizing alternative fuels such as refuse-derived fuel (RDF) and solid recovered fuel (SRF) can gain a substantial competitive edge. In many cases, however, input waste streams contain diverse materials not suitable for co-processing in the cement kiln. A well-designed alternative fuel production process ensures the best quality. To maximize energy production with the lowest possible emissions, a homogeneous grain size, high calorific value, controlled material composition, removal of fines, low chloride and a stable humidity content are a must. Opening waste bags and reducing the size of waste by pre-shredding ensures that unwanted items can be screened and separated from the process. Later in the process, when you have achieved an optimal material content for the
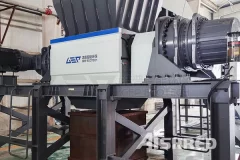
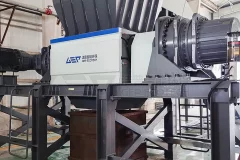
Many processes of co-processing municipal solid waste in cement kilns mostly adopt the method of shredding the waste and then incinerating it in the kiln. Since the municipal solid waste is mixed waste, in order not to affect the cement clinker calcination process and product quality, improve the acceptance ability and control ability of the cement kiln system, shredder machine must be set up. So what kind of shredder is used for pre-processing and co-processing MSW in the cement industry? Today, I recommend a GD series MSW shredder for your reference. GD series double-shaft shearing MSW shredders use the principle of mutual shearing and tearing between two relatively rotating knives to shred materials. Adopt "double motor + double planetary reducer", with strong power and high running stability. It is often used in environmental protection fields such as municipal solid waste disposal, resource regeneration, and waste incineration pretreatment. The equipment has the characteristics of low speed, large