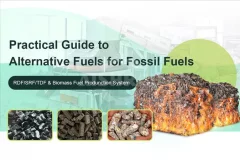
Practical Guide to Alternative Fuels for Fossil Fuels, RDF/SRF/TDF & Biomass Fuel Produnction System
2025-03-26We specialize in the design and manufacturing of efficient, environmentally friendly Solid Recovered Fuel (SRF) and Refuse-Derived Fuel (RDF) processing equipment. Our state-of-the-art production lines transform various waste materials into high-quality alternative fuels, effectively addressing waste management challenges while delivering sustainable energy solutions for businesses.
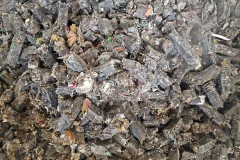
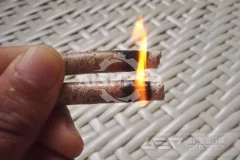
To answer the question of 'how much does it cost to produce one ton of alternative fuel', it is necessary to analyze and think from multiple perspectives. The following is a step-by-step analysis process:1. Definition and classification of alternative fuelsAlternative fuels refer to the use of combustible waste to replace traditional natural fossil fuels for production. The application of combustible waste in industry can not only save energy, but also contribute to environmental protection. Common alternative fuels include garbage derived fuel (RDF), solid recycled fuel (SRF), tire derived fuel (TDF), biomass fuel, and municipal sludge.2. Economic analysis of alternative fuelsThe economy of alternative fuels depends not only on production costs, but also on their calorific value and comparison with fossil fuels. According to relevant information, the calorific value of alternative fuels is usually lower than that of coal, but by increasing the calorific value and reducing the heat loss coefficient ratio,
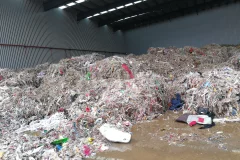
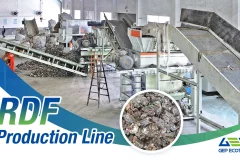
In the pulp and paper production process, will produce a variety of solid waste (i.e., slag), for example, an annual production capacity of 1 million tons of paper mills, the amount of slag accounted for about 10% of the amount of slag, i.e., 100,000 tons / year, which is a large number, and highly concentrated, such as improper disposal, but also cause significant pollution and endanger the ecological environment. The composition of paper production waste is very complex, mainly contains: rope, cotton yarn, cotton cloth, paper residue, wood chips, rubber, plastic, electronic parts, wire, nails, aluminum cans, PE plastic bottles, waxed paper and glass, stone and sand. Paper waste residue can be used to make solid alternative fuels, a utilization that not only reduces waste, but also replaces traditional fossil energy sources and reduces carbon emissions. The plastics in paper production waste can not be degraded, and direct stacking seriously affects the ecological environment. At present, there are paper
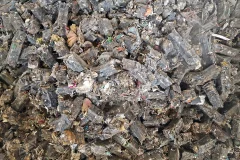
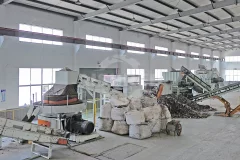
Alternative Fuels (SRF&RDF) - a New “Breakthrough” in the Recycling of Industrial Solid Waste
2024-10-03Alternative fuels (SRF/RDF), as a renewable energy source with broad prospects for cement kilns, fluidized beds and other various industrial kilns, have become the fourth largest energy source after coal, oil and natural gas, and have considerable importance. Focus on the advantages of alternative fuels (SRF/RDF):As a clean and environmentally friendly renewable resource, alternative fuel (SRF/RDF) is itself processed from solid waste garbage, with similar combustion efficiency to fossil fuels, but with low carbon emissions, which meets the policy requirements of carbon emission reduction, saves costs for enterprises and is significant for environmental protection. Industrial Solid Waste Treatment Line:AI Shred has developed an industrial solid waste processing line with a modular design that converts industrial waste into high quality, high calorific value alternative fuels (SRF/RDF) that can be used to replace non-renewable fossil energy sources for fuel use. For more complex wastes, the quality of the
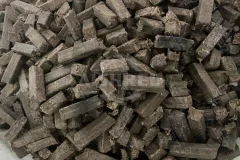
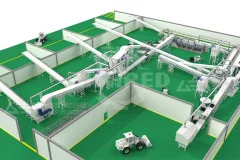
Normally, heavy materials such as broken bricks and concrete in c&d scrap are crushed and sorted into recycled aggregates and reused in the construction and building materials industry to achieve resource utilization. However, light materials such as wood chips, paper, cloth, and plastic are piled up and left idle because their components are too complex, sorting is too laborious, and disposal is too difficult, which not only increases the operating burden of enterprises, but also causes a waste of these resources.So is there a perfect solution to this problem? Of course, turning c&d scrap light materials into alternative fuels is a good way out.Process of C&D Scrap Light Materials Alternative Fuel ProductionThe process of turning C&D scrap light materials into alternative fuel involves several steps. Initially, the waste materials are collected and transported to a processing facility. At the facility, mechanical processing techniques, including shredding, grinding, and sorting, are employed to reduce the
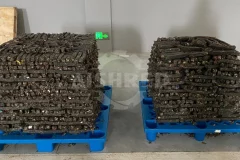
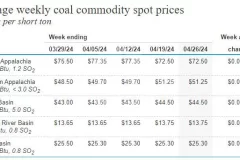
What is the price of RDF/SRF?
2024-05-06The pricing of RDF (Refuse-Derived Fuel) and SRF (Solid Recovered Fuel) per ton is a significant concern for investors and users alike. It goes beyond just investment returns, impacting the operational costs of users directly. Much like coal pricing, RDF/SRF pricing varies based on factors such as its source, quality, and market dynamics.RDF-5 PelletsThe U.S. Energy Information Administration website outlines prices for different coal grades and sulfur content, highlighting the disparities in coal pricing. When considering RDF/SRF for fuel application, factors like calorific value, post-combustion emissions, and potential impacts on the environment or end products are crucial. For example, RDF with high chlorine content may affect concrete quality when used in cement kilns.Average weekly coal commodity spot pricesHowever, determining RDF/SRF pricing is more complex than coal pricing. Firstly, there's no specialized RDF/SRF category in the spot or futures market. Secondly, RDF/SRF comes from various sources
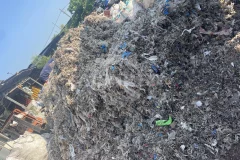
The pulp and paper industry, while essential for producing everyday products, also generates substantial amounts of waste, including rejects and by-products. Addressing this waste is paramount for sustainability efforts within the industry. One promising avenue is utilizing shredding technology to process these rejects into alternative fuel sources.The Challenge of Pulp and Paper Factory RejectsPulp and paper factories produce rejects in various forms, such as off-specification paper rolls, trimmings, pulping rejects, and packaging waste. Managing this waste is a significant challenge due to its volume and diverse composition. Traditional disposal methods like landfilling or incineration are not only environmentally detrimental but also inefficient in harnessing the potential energy locked within the rejects.Shredding as a SolutionShredders offer an effective means of transforming pulp and paper factory rejects into alternative fuel sources. By breaking down rejects into smaller, uniform pieces, shredding
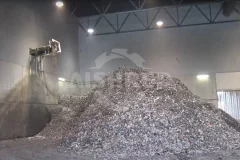
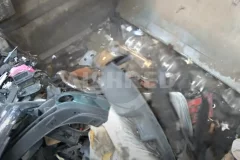
As industries worldwide seek sustainable alternatives to traditional fuel sources, cement plants are turning to innovative solutions such as alternative fuels. Shredders play a crucial role in this transition, enabling the efficient processing of diverse waste materials into valuable fuel sources. This article explores the integration of shredders in cement plants for alternative fuel production, highlighting the benefits and advancements in sustainable energy practices.The Need for Alternative FuelsCement production is energy-intensive, relying heavily on fossil fuels such as coal and petroleum coke. However, the environmental impact of fossil fuel combustion, including greenhouse gas emissions and air pollution, necessitates the adoption of alternative fuels. Alternative fuels derived from waste materials offer a sustainable solution, reducing reliance on finite resources and mitigating environmental impact.Role of Shredders Shredders are indispensable equipment in the production of alternative fuels for
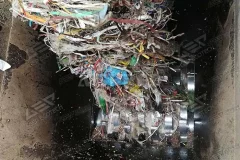
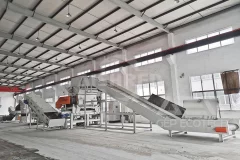
In the pulp and paper production process, it will produce a variety of solid waste (i.e., slag), for example, an annual production capacity of 1 million tons of paper mills, the amount of slag accounted for about 10% of the amount of slag, i.e., 100,000 tons / year, which is a huge number, and highly concentrated, such as improper disposal, but also cause significant pollution and endanger the ecological environment. The composition of paper waste is very complex, mainly contains: rope, cotton yarn, cotton cloth, paper residue, wood chips, rubber, plastic, electronic parts, wire, nails, aluminum cans, PE plastic bottles, waxed paper and glass, stone and sand. Paper waste residue can be used to make solid alternative fuels, a utilization that not only reduces waste, but also replaces traditional fossil energy sources and reduces carbon emissions.The plastics in paper waste residue cannot be degraded, and direct stacking seriously affects the ecological environment. At present, there are paper waste separation
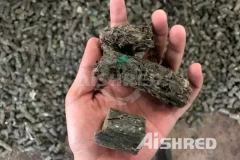
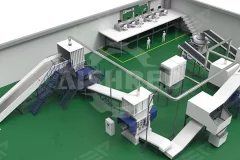
Alternative Fuels RDF&SRF Treatment Systems
2024-02-25Solid alternative fuel RDF/SRF is a solid form of fuel made from industrial solid waste through various processes. By reducing the water content of industrial waste and increasing the calorific value of the product, it replaces traditional energy sources (coal) and reduces pollutant emissions, thus realizing "turning waste into treasure".Energy Structure and ProspectsFrom the perspective of energy structure, alternative fuels (SRF/RDF), as a renewable energy source with broad prospects, are processed from solid wastes, with combustion efficiencies similar to those of fossil fuels, but with low carbon emissions, and are generally utilized in existing thermal power plants, cogeneration plants, and cement kilns to carry out coupled power generation/blending power generation/mixing power generation/co-disposal in cement kilns with RDF/SRF, which saves costs for enterprises and contributes to the environmental protection.The substitution relationship between fossil fuels and alternative fuels (SRF/RDF) is:- 1.4
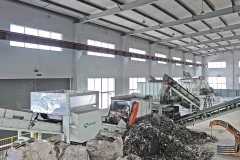
Solid Waste Disposal System by GEP Helps Cement Kiln Reduce Costs and Increase Efficiency
2023-12-24GEP ECOTECH has always been committed to the treatment of various solid waste, and has rich experience in operating projects in the preparation of alternative fuels for cement kilns. It can provide professional solutions and high-performance equipment for the green transformation of cement enterprises.1. Cement kiln collaborative disposal of solid waste technologyCement kiln collaborative disposal of solid waste technology uses solid waste to replace some raw materials or fuels, enabling cement production enterprises to save on raw material demand, reduce energy consumption, and achieve complete resource utilization. At the same time, the carbon dioxide released by the decomposition of calcium carbonate is reduced, saving on the occupation of waste landfills. It meets the requirements of energy conservation, consumption reduction, and emission reduction, and has significant economic and environmental benefits.2. What are the sources of alternative fuels for cement kilns?Alternative fuels refer to fuels that
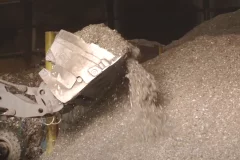
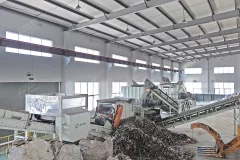
When it comes to discarded shoes, many people think about how to properly dispose of them, and one potential solution is to convert old shoes into solid recovered fuel (SRF). Although this may sound surprising, in theory, this approach is possible. Here are some considerations for converting old shoes into solid recovered fuel .Why can old shoes be used as solid recovered fuel ?Discarded shoes contain a variety of materials such as rubber, leather, synthetic fibers and metal trimmings. The processing and utilization of these materials, especially the combustion potential of rubber and synthetic fibers, makes discarded shoes a potential solid recovered fuel .Advantages of using old shoes as solid recovered fuelHigh calorific valueSmall particle sizelow moisture contentManufacturing process of using old shoes as solid recovered fuelPrimary shredding (shred to 30 mm),Screening to remove fine materials (helps reduce moisture content), trommel screen recovery or air density separation to remove heavy components,
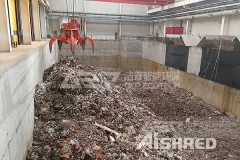
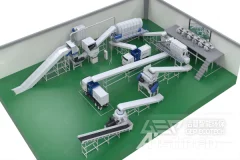
Recently, many customers have inquired whether it is possible to convert all MSW (Municipal Solid Waste) into high calorific value RDF? Here, it should be explained that in the field of MSW classification, many countries and regions currently do not reach the level of complete segmentation. MSW is still mixed with a large amount of kitchen waste, as well as low calorific value non combustible materials such as porcelain chips and stones. It is impossible to make such materials into high calorific value alternative fuels. Therefore, before MSW can be converted into alternative fuels, a series of shredding and screening equipment must be used to separate the non combustible materials inside, and the remaining combustible materials can be processed into high calorific alternative fuels RDF/SRF.The specific disposal process is as follows: MSW is transported to the MSW disposal center through specialized transportation vehicles, first dumped into the waste storage pit in the disposal center, and then collected
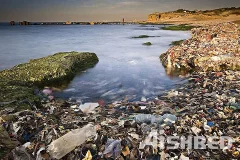
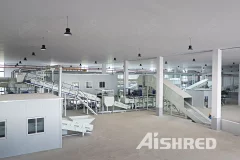
Mixed municipal waste contains a large number of recyclable beverage bottles, metals, cardboard and other renewable resources that can be recycled and reused; the content of perishable waste, mainly food waste, accounts for 40-60%, which can be utilized as a biomass energy source; and the largest proportion is still high-calorific-value combustibles, which can be prepared as "alternative fuels (RDF/SRF)" to reduce the use of coal combustion.AIShred, as a manufacturer of solid waste pre-processing equipment, offers a complete range of proven and reliable systems and equipment for the preparation of alternative fuels (SRF) based on the three main pre-processing objectives of mixed domestic/other waste: "sorting of recyclables", "extraction of organic matter", and "preparation of combustible materials for RDF/SRF".The whole set of domestic garbage alternative fuel (SRF) preparation system adopts the automatic process design of "feeding - bag breaking - screening - recycling - crushing - transportation", which
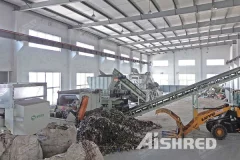
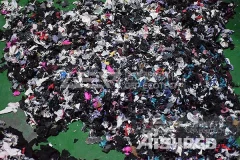
SRF Alternative Fuel Disposal Process
2023-08-21SRF is the abbreviation for Solid Recovered Fuel. SRF is usually a refined RDF (Refuse Derived Fuel). SRF is not waste, but a clean, homogeneous, high-quality, and high calorific value fuel that can be used in power plants or cement plants to replace traditional fossil fuels such as coal. Moreover, SRF is a kind of environmentally friendly fuel, with carbon dioxide emissions only one-fourth that of coal, and NOx emissions significantly reduced.Component analysisSRF is usually composed of papermaking waste, waste wood, biomass fuel, combustible materials in MSW (Municipal Solid Waste), and waste textiles in general industrial solid waste.Process flowFirstly, the material is transported to a primary double shaft shearing shredder, which shreds the material into smaller sizes of around 100-300mm. Then these materials enter the magnetic separator, through which the ferromagnetic metals inside the materials are recycled. The remaining materials are transported to a secondary single shaft fine shredder, which
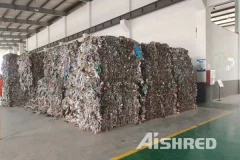
Alternative Fuel System for Cement Industry
2023-07-21With the global demand for cement on the rise, the cement industry faces an imperative to adopt sustainable practices that minimize its environmental impact. In this pursuit, the industry has strategically prioritized the search for alternative fuels, a crucial step towards reducing fossil energy consumption, improving manufacturing processes, curbing pollution, and cutting down production costs. Leading the charge in environmental technology solutions, GEP ECOTECH is at the forefront of driving sustainability in cement production. Their cutting-edge Alternative Fuel System offers a comprehensive and proven technology that efficiently converts various materials with calorific value into engineered fuels. This groundbreaking system incorporates shredding, sorting, screening, conveying, and control mechanisms, ensuring a streamlined and efficient process with an impressive single production line capacity of up to 80 tons per hour. GEP ECOTECH's Alternative Fuel System serves as a game-changer in cement
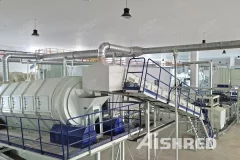
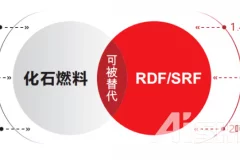
During the production of cement, clinker needs to be calcined at a high temperature of 1300-1450°C, which will consume a large amount of fossil energy, and the carbon dioxide produced by the combustion of fossil fuels accounts for about 30%-35% of the total carbon emissions of cement companies. The application of alternative fuels to reduce the use of coal has received attention in the cement industry and can significantly reduce the carbon emissions from fuel combustion. As a promising renewable energy source, alternative fuels (SRF/RDF) have become the fourth largest energy source after coal, oil and natural gas for various industrial kilns such as cement kilns and fluidized beds. Alternative fuels as a high-quality environmentally friendly renewable resources, itself from solid waste waste treatment, combustion efficiency and fossil fuels similar, but low carbon emissions, to meet the policy requirements of carbon emission reduction, cost savings for enterprises, has an important significance for
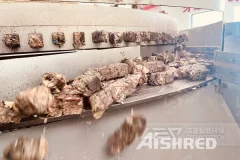
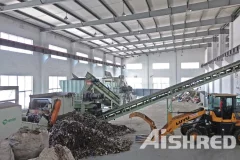
Fuel Production From Household Waste
2023-05-22In recent years, the popular term "RDF" in the field of solid waste refers to waste derived fuels, and most environmentalists have also turned their attention to the field of household waste. The composition of household waste we usually refer to is a mixture of wet waste and dry waste, while in the preparation of fuel for household waste, it is best to make a distinction based on current incineration needs. Frontend differentiation can reduce the investment cost of pre-treatment production lines while also improving the calorific value of materials. In the field of incineration, calorific value is a sensitive term. In fact, this process flow is not complicated. Our designed process principles have three positioning points: "impurity removal, reusable selection, and combustible compression". These three process points constitute the equipment solutions applicable in the current field of solid waste disposal. The impurity removal we refer to can be understood as the purification of household waste. There will
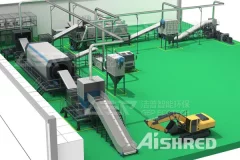
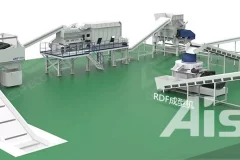
"Eat" into waste, "vomit" out of fuel, and become a "artifact" that turns waste into treasure in Zhengzhou, Henan. The Industrial Solid Waste Disposal System produced by GEP ECOTECH can "eat" 20 tons of C&I waste in one hour and produce preparations Popular alternative fuel RDF/SRF. So what craftsmanship does GEP ECOTECH make "people suspected" and make the waste into the "fragrant" of the fuel industry?Waste is an abandoned item that loses its value and cannot be used. It is the ultimate part of the material cycle. The widely used waste treatment methods today are sanitary landfills, high temperature compost and incineration. However, most of the industrial waste incineration contains considerable heat values, and directly landfills or incineration undoubtedly causes waste of resources. Now, this industrial solid waste disposal system located in Zhengzhou, Henan can effectively use general industrial solid waste such as leather edge, cloth edge corner, waste paper residue, waste fabric, waste plastic, etc
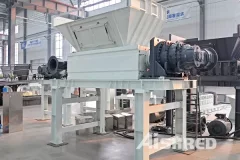
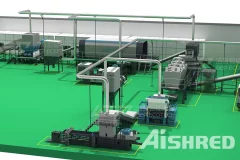
Industrial waste realizes its final value in factory production and is hidden in the corners of factories because there is no way to be discarded directly, plus the high price of disposal. In the "double carbon" target, high coal prices, cement companies increasingly hot competition and other comprehensive background, alternative fuels and co-disposal has received more and more attention, the wave of industrial solid waste preparation of alternative fuels was born. AI Shred environmental protection alternative fuel preparation technology can turn industrial solid waste into reusable "coal" energy, industrial waste disposal is no longer a problem!What are the categories of industrial waste?Industrial waste is divided into cloth and leather trimmings from garment factories and shoe factories, waste residue from paper mills and twisted rope braid material, fiberglass trimmings, waste rubber and plastic, etc. From the perspective of resource recycling, these wood materials to leather trimmings, they can all be
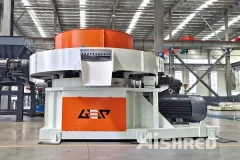
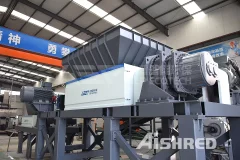
RDF Shredders for Waste-to-Fuel
2023-02-14Derived fuel has the characteristics of high calorific value, stable combustion, easy transportation, easy storage and low secondary pollution, which is widely used in drying engineering, cement manufacturing, heating engineering and power generation engineering. RDF raw materials mainly come from domestic waste, industrial waste, organic waste, etc. It contains waste paper, hard plastic, metal, glass, wood, rubber and other substances. The coarse shredder and fine shredder meet the crushing requirements of RDF, greatly simplifying the RDF treatment process and realizing high economic and ecological value. Equipment Configuration The crushing of this high mixture of materials places high demands on the crushing technology. The stable operation of the shredder requires high performance alloys and high reliability of the whole machine. This type of crushing requires a machine capable of handling hard materials such as metals and plastics. To obtain a high quality RDF, the following steps need to be performed:
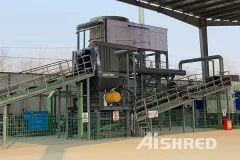
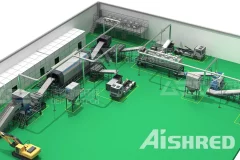
With the development of the economy, the number of waste textiles eliminated by residents has gradually increased, sporadic treatment cannot meet the production requirements, and a sustainable industrial waste system is urgently needed to help us explore together. Today, let's talk about the energy recovery of waste textiles. Because of the addition of comprehensive materials, the thermal value of the waste textiles is very good and the combustion is good. Therefore, it has great potential for incineration power generation and cement kiln. As the energy recovery of waste textiles, we must use industrial waste shredding to deal with the production line. Only through the disposal of this production line can we meet the energy recovery of waste textiles. So what is this industrial waste system? First of all, the core equipment of this system is shredding+sorting, and the connection system is conveying. The purpose of broken is to fully shatter, shear and crushed materials. First, ensure that the material can be
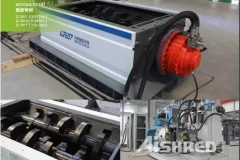
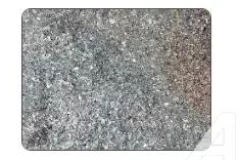
AIShred RDF&SRF Alternative Fuel Technology
2022-07-12Internationally, Refuse Derived Fuel (hereinafter referred to as "RDF") is regarded as a new way of waste harmless, recycling and reduction. It has been widely used in cement, power generation and other industries. It is green, environmentally friendly, high quality and low price Alternative fuels (SRF/RDF) are the new trend of the future. The preparation of waste-derived fuel RDF is not limited by site and scale. It is suitable for small and medium-sized waste treatment plants to be scattered and manufactured, and then collected for power generation, which is conducive to improving the scale and efficiency of waste-to-energy power generation. Converting waste to waste-derived fuel (RDF) serves two purposes: it can reduce the amount of waste sent to landfills, thereby solving problems in the waste field, and it can supply large coal-fired power plants, waste incineration plants, cement plants Provides a large number of alternative fuel RDF. AIShred RDF&SRF Alternative Fuel Achievement PathAIShred has
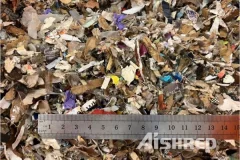
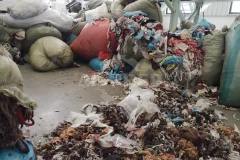
Solid Waste to Engineered Fuel Solution
2022-05-27Engineered fuel is a kind of alternative fuel produced by processing and blending construction and demolition material, and/or select industrial and/or commercial byproduct material streams including: plastic, paper, paper mill contraries, paper fiber, cardboard, textiles, carpet, and rubber.Waste to Engineered Fuel Processingpre-screening of potential customers' material before it is received;feedstock acceptance practices to ensure a primarily wood-based product and removal of materials that may have high contaminant levels;removal of metals and fines;manual sorting to remove residual contaminated material;shredding to improve the fuel characteristics of the material;final screening to ensure consistency and low ash levels and improved combustion in the fuel.GEP ECOTECH Shredding Solution in Waste-to-Fuel ApplicationShredding is the most important stage in Waste-to-Fuel applications, as it imporve the fuel characteristics. GEP ECOTECH offers two kind of shredders for waste to engineered fuel application: