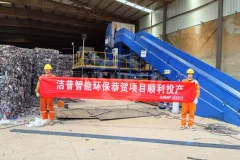
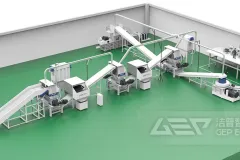
The traditional RDF (Refuse-Derived Fuel) production process mainly relies on heavy-duty single shaft shredders for shredding treatment, sometimes using double shaft shearing or primary shredding as pretreatment equipment to improve material processing efficiency. However, this process presents many challenges: the price of single shaft shredders from some world well-known manufacturers may reach as high as USD850,000, putting significant financial pressure on small and medium-sized enterprises in the initial investment stage; The power consumption for ton processing can reach 50 kW·h, which not only increases operating costs, but may also require additional procurement of high-capacity transformers to meet demand; In addition, wearable parts such as cutters wear out quickly and often require repair or replacement within a few days, thereby increasing maintenance costs. These factors limit the cost control and production efficiency of traditional process, affecting the long-term sustainable development of
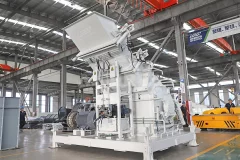
A cement plant in Mexico is in need of textile cutting equipment to process air bags, which are primarily made from nylon and hard plastic-fabric. The required equipment with a processing capacity of 1 to 2 tons per hour (TPH) and an output size of less than 30mm.At GEP ECOTECH, we specialize in providing efficient and tailored solutions for challenging material processing needs. After reviewing the requirements, we would like to recommend our GSS15 Single-Shaft Shredder as the optimal solution for your air bag processing needs.Why Choose the GSS15 Single-Shaft Shredder?High Torque and Durability:The GSS15 is equipped with a high-torque motor that provides the necessary power to shred tough, dense materials like air bags. The high-torque operation ensures that the shredder effectively cuts through the tough nylon and plastic layers without causing jams or excessive wear.Adjustable Output Size:The GSS15 comes with adjustable cutting blades, allowing you to achieve the desired particle size of
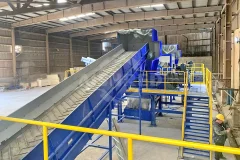
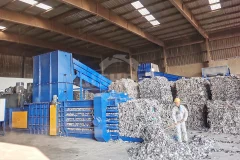
In the economically dynamic Yangtze River Delta region of China, a waste textile alternative fuel production line with an annual capacity of 100,000 tons is set to be commissioned. This innovative production line will provide efficient and environmentally friendly RDF (Refuse-Derived Fuel) to a cement kiln operated by a state-owned enterprise, replacing traditional coal and significantly reducing greenhouse gas emissions. The project not only accelerates the green transformation of the cement industry but also stands as a key development in the circular economy sector.The Yangtze River Delta is a global hub for textile and garment production, generating vast quantities of clothing each year, which inevitably results in substantial textile waste. Effectively managing this waste has long been a challenge. This 100,000-ton per year alternative fuel production line converts waste textiles into high-energy RDF fuel, addressing the local processing capacity shortage while reducing fossil fuel usage. The project
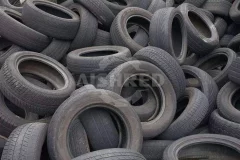
Recently, an Australian customer inquired about a 4-6 ton per hour tire pelletizing line, the majority of which are car and truck tires, with diameters of up to 1200mm, and a discharge size of 150mm containing steel wire, to be used as an alternative fuel for cement kilns to burn to generate energy. The client is an Australian company specializing in import and export, providing integrated solutions with financial, environmental and operational objectives for a variety of sectors including industrial and commercial construction. After initial communication, it was determined that the project is currently in the stage of technical improvement and supplier selection, our company according to the requirements provided by the customer and the existing operation of the site problems, to give targeted solutions to address the customer's main concerns and timely provision of equipment programs and quotations. Then it enters the repeated communication link, at present the customer gives high evaluation and
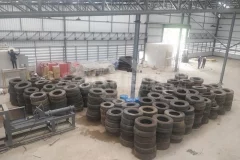
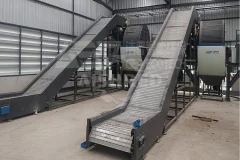
What Would a Tire Granulating Line Be Like?
2024-09-29Recently, a Latin America customer inquired about a 5-ton per hour tire granulation line project, of which 90% are car tires, and the rest are truck tires, tractor tires, bus tires, etc., but the diameter does not exceed 1200mm. The customer's requirements for the discharge particle size are relatively wide, and they have the following applications:1. Around 50x50mm, to be used as a substitute fuel for cement kilns and generates energy through combustion2.<1mm, to be used as rubber powder for fine sand and mortar for construction, or for sewage treatment3. from 2 to 5mm, to be used as a medium: coarse sand for reinforced concrete, paving, and asphalt productionThe client is a turnkey engineering company that provides comprehensive solutions with financial, environmental, and operational goals for various fields such as industry, shopping centers, hospitals, and commercial buildings. After preliminary communication, it has been determined that the project is currently in the feasibility study stage, and our
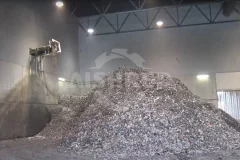
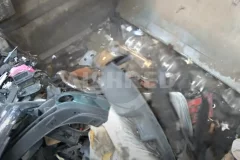
As industries worldwide seek sustainable alternatives to traditional fuel sources, cement plants are turning to innovative solutions such as alternative fuels. Shredders play a crucial role in this transition, enabling the efficient processing of diverse waste materials into valuable fuel sources. This article explores the integration of shredders in cement plants for alternative fuel production, highlighting the benefits and advancements in sustainable energy practices.The Need for Alternative FuelsCement production is energy-intensive, relying heavily on fossil fuels such as coal and petroleum coke. However, the environmental impact of fossil fuel combustion, including greenhouse gas emissions and air pollution, necessitates the adoption of alternative fuels. Alternative fuels derived from waste materials offer a sustainable solution, reducing reliance on finite resources and mitigating environmental impact.Role of Shredders Shredders are indispensable equipment in the production of alternative fuels for
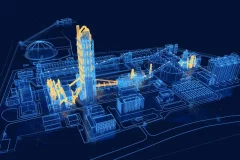
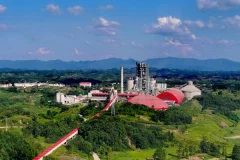
In the quest for sustainability and reduced environmental impact in cement production, Alternative Fuel and Raw Materials (AFR) play a pivotal role. AFR refers to the use of non-conventional materials as a substitute for traditional fuels and raw materials in cement manufacturing. These materials typically include various types of waste, such as industrial by-products, biomass, or non-recyclable materials, which would otherwise end up in landfills. The integration of AFR in cement kilns not only helps in managing waste effectively but also significantly reduces the reliance on fossil fuels, leading to lower carbon emissions. The utilization of AFR is a complex process, involving careful sourcing, processing, and compatibility assessment with existing cement production technology, all aimed at maintaining the quality of the cement while ensuring environmental compliance.Fuel may vary from Liquid, Semi solid or Solid from Biomass, Paint sludge, MSW, Tyre chips,Pharmaceutical wastes etc. which are having
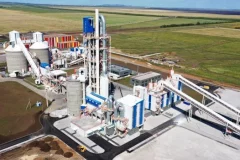
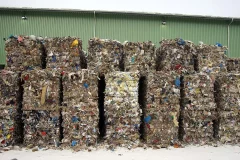
Cement Plant Refuse Derived Fuel System
2024-01-03The cement industry is undergoing a positive and remarkable transformation: replacing fossil fuels with refuse derived fuels (RDF), solid recover fuels (SRF) or biomass. This measure helps to reduce carbon emissions, achieve more environmentally friendly cement production processes, and fulfill the commitment of cement enterprises to sustainable development.GEP ECOTECH is committed to promoting sustainable development in the cement industry, and we offer a variety of innovative alternative fuel solutions for this purpose. Our solutions cover various kinds of materials and feeding requirements, tailoring the best solutions for customers to ensure stable and high-quality fuel supply.Shredding SystemA powerful shredding system is the key to the successful production of high-quality RDF/SRF. GEP ECOTECH's multi-stage shredding system doesn't fear the challenges of complex materials. From pre shredder to shearing shredder, and the eye-catching single shaft shredder, our shredders' durability and trouble free
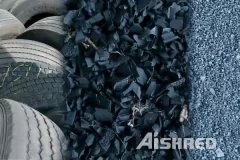
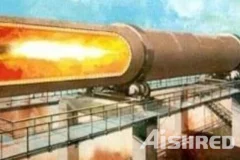
Conventional fuels like hard coal and lignite that are commonly used fuels in cement production have high specific CO2 emission values (Hard coal: ~95 kg CO2/GJ; Lignite: ~98 kg CO2/GJ). Consequently, substituting these with other fuels having lower specific emssion values (e.g. fuel oil or natural gas) or with other sources that can satisfy the thermal demand of the processes is an effective way of reducing CO2 emissons. Principally, in cement kilns conventional fossil fuels can be substituted up to 100% by alternative fuels. Nevertheless, there are certain technical limitations like the calorific value, the moisture content, and the content of side products like trace elements or chlorine. The calorific value of most organic material is comparatively low (10 – 18 GJ/t). For the main firing of the cement kiln an average calorific value of at least 20-22 GJ/t is required, meaning that high calorific alternative fuels are mostly used in the main firing. Waste tyres can be used as a fuel in cement kilns. Waste
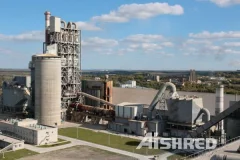
Co-processing Waste in Cement Industry
2022-04-21The problem of waste is one of the most urgent on the world agenda, According to the World Bank, the world generates 2.01 billion tonnes of waste every year, with at least 33 percent of that—extremely conservatively—not managed in an environmentally safe manner. Therefore, the most important task is to clear the waste and create a system that will allow separating waste, competently managing its flows, processing it and without harm to nature. Turning the so-called “tailings” into cement, which remain at the waste sorting complexes after the extraction of all useful recyclable materials, is one of the most environmentally friendly and effective solutions to this problem. The use of alternative fuels from municipal solid waste (MSW) in cement production will help global achieve environmental goals.Waste Disposal in the Production of CementLimestone, clay and thermal energy are needed to make cement. The cost of the latter is 30% of all production costs. The cement industry uses a variety of fossil fuels to
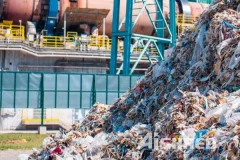
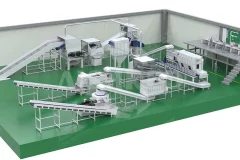
Due to the continuing energy cost fluctuations and the discussions on the sustainable protection of resources the cement industry has hardly enabled to reduce its entire energy and power demand as a result of technical optimisation of its cement production. With the rising energy prices, people have successively used petroleum and coal as the main fuel for cement production. Later, people began to explore the use of waste oil and tires. Nowadays, as people pay more and more attention to reducing carbon emissions, the waste-to-fuel technology has become more and more mature, and many cement kilns have begun to use municipal solid waste or industrial and commercial waste as alternative fuels.Substituting Coal and Petcoke with Alternative fuelsCoal and petcoke, two of the most carbon-intensive fuels, are typically used to heat cement kilns. The substituting coal with lower-carbon fuels offers the greatest short-term potential to reduce CO2 emissions in the industry. Most alternative fuels have a lower carbon
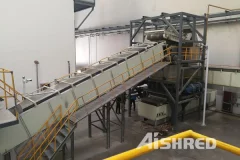

Industrial Shredder for Cement Industry
2022-04-06Cement production is an extremely energy-intensive process that emits approx. 8% of the world’s CO2. There are huge economic and environmental benefits to be made by replacing fossil fuels with alternative fuels made from waste. Cement producers utilizing alternative fuels such as refuse-derived fuel (RDF) and solid recovered fuel (SRF) can gain a substantial competitive edge. In many cases, however, input waste streams contain diverse materials not suitable for co-processing in the cement kiln. A well-designed alternative fuel production process ensures the best quality. To maximize energy production with the lowest possible emissions, a homogeneous grain size, high calorific value, controlled material composition, removal of fines, low chloride and a stable humidity content are a must. Opening waste bags and reducing the size of waste by pre-shredding ensures that unwanted items can be screened and separated from the process. Later in the process, when you have achieved an optimal material content for the