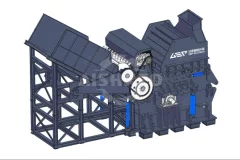
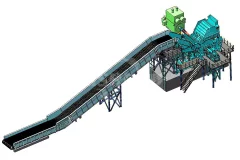
Scrap Aluminum Hammer Shredding Production Line Production line introductionScrap Aluminum Shredder is a kind of shredding equipment used to process scrap aluminum, which is mainly used for the shredding and sorting operation of machined aluminum, raw aluminum, aluminum alloy and broken aluminum. With advanced technology, large processing range and high production efficiency, the production line can fully separate iron, aluminum and plastic, and the purity can reach more than 99%, and the production process is noiseless and non-polluting, which is the mainstream equipment for scrap aluminum recycling at present. Process FlowScrap aluminum shredding and sorting equipment consists of scrap aluminum shredder, magnetic separator, trommel screen, eddy current sorter and dust collector. The material is sent into the aluminum shredder for fine shredding through the conveyor, and the shredded material is separated from iron by the magnetic separator, and then it enters into the trommel screen to separate the
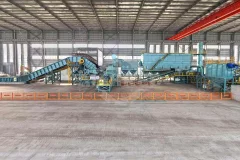
Scrap Steel Hammer Shredding Production Line
2024-11-19Scrap steel shredding production line is used to process scrapped car body, tinplate, old home appliances, bicycle and electric car frame, can briquettes and other light and thin wastes to make them into pure raw materials for steel making. Through continuous shredding and extrusion, it can remove impurities, increase the specific gravity of heap, reduce the cost of transportation and smelting, and meet the requirement of “fine material into the furnace” of the steel mill.Scrap steel shredding production line has advanced technology, large processing range, high production efficiency, can sort out the non-ferrous metals, remove non-metallic inclusions, processing of high-quality scrap steel with high purity, and less environmental pollution in the process. Scrap steel processed through the scrap shredding production line is clean and high-quality scrap steel, its natural bulk density of 1.2 ~ 1.7t/m3, is the ideal steelmaking furnace material.Process flowScrap steel shredding production line consists of
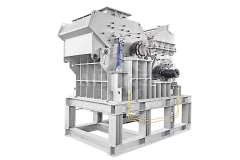
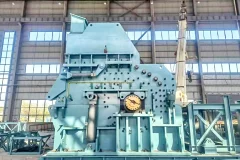
Hammer Shredder
2024-10-08Hammer shredders, also known as hammer mills, are powerful and versatile machines widely used in the recycling industry for efficiently reducing various materials, particularly waste metals, into smaller, manageable pieces. With their high horsepower and large throughput capacity, hammer shredders are among the most commonly used equipment in waste recycling plants and metal recovery facilities. While they excel at processing loose materials, hammer shredders are not suitable for compacted waste, for which GEP ECOTECH's heavy-duty debalers are recommended for pre-processing.GEP ECOTECH's heavy-duty hammer shredders are high-performance solutions designed to meet the demanding needs of recycling operations. Their rugged design and powerful capabilities make them ideal for handling large volumes of difficult materials, including automobile shells, white goods, and both ferrous and non-ferrous metals. These machines are built for continuous operation with minimal downtime, providing cost-effective and reliable
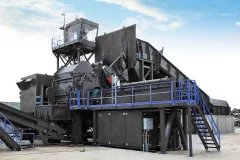
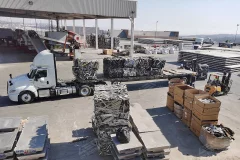
When it comes to metal processing and waste management, the Hammermill Shredder is an essential piece of equipment. It is widely used for shredding discarded metal materials such as automotive wreckage, discarded electronic devices, and other metal scraps into smaller particles for further recycling or disposal.Working Principle of the Hammermill ShredderThe Hammermill Shredder operates based on a set of rotating hammers that crush metal materials at high speeds. It shreds metal waste into smaller particles through impact and shear forces. The primary function of a Hammermill Shredder is to reduce large metal pieces into smaller, manageable fragments. It is particularly effective in breaking down bulky metal waste, such as automotive parts or appliances, into smaller particles. Hammermill Shredders typically have a single rotor with multiple hammers mounted on it. The hammers strike the metal waste as it passes through, resulting in fragmentation. Hammermill Shredders are commonly used in the initial stages

Glass Crushing & Recycling Machine for Sale
2023-07-20Glass, a versatile and widely used material, holds tremendous potential for recycling and reuse. Embracing the principles of circular economy, glass recycling offers a multitude of environmental and economic benefits, including reduced reliance on natural resources, minimized energy consumption, and mitigated waste impact on the environment. In pursuit of a cleaner and greener future, we have developed cutting-edge glass crushing equipment that facilitates efficient glass recycling, enabling crushed glass to be returned to the furnace for reuse or repurposed as sand. Our glass crushing equipment caters to the diverse needs of the recycling industry. The crushed glass can either be reintroduced to the glass furnace, where it is melted down and molded into new glass products, or transformed into high-quality sand. This versatility ensures that glass waste is given a new lease on life, contributing to resource conservation. The test video showcases our revolutionary Hammer Mill in action, demonstrating its
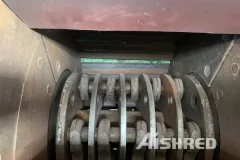
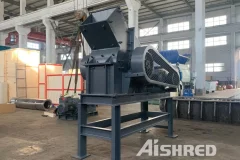
Hammer Mills for Waste and Recycling
2022-06-18A hammermill is a common type of equipment currently used for size reduction of solid waste. A hammermill consists of a central rotor or shaft with radial arms (hammers) protruding from the rotor circumference. The rotor is enclosed in a heavy duty housing, which may be lined with abrasion resistant steel members. Some hammermilIs may also have stationary breaker plates or cutter bars mounted inside the housing. Input material is reduced in size by impact, attrition, and shearing forces induced by the hammers. There are two basic types of hammermiIls: the horizontal shaft type and vertical shaft type. The horizontal shaft hammermill is the more common type. As the name implies, the rotor or shaft is horizontal and supported on each end. Input is usually at the top and material flows through the machine assisted by gravity. Force feed at the side of the hammermill has also been used for solid waste shredding. Most horizontal hammermiIls have a grate placed across the output opening. Input material cannot pass
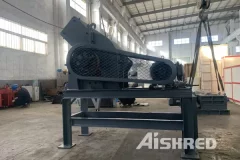
AIShred Launches its New Hammer Mill Series
2022-06-06Hammer mills work on the principle that most materials will crush, shatter, or pulverize upon impact. Material is fed into the mill’s chamber through the feed chute, typically by gravity, where it is struck by ganged hammers attached to a shaft that rotates at high speed inside the mill’s grinding chamber. The material is crushed or shattered by a combination of repeated hammer impacts, collisions with the walls of the grinding chamber, and particle on particle impacts. Perforated metal screens or bar grates covering the discharge opening of the mill retain coarse material for further grinding, while allowing properly sized materials to pass. AIShred offers an extensive line of hammer mills suitable for a wide variety of applications, and include wood grinders, industrial, full circle screen, and laboratory scale styles. Most models are available in gravity or pneumatic discharge.High Production Hammer MillProvides the tip speed required for maximum throughput. Easy to change screens produce the exact