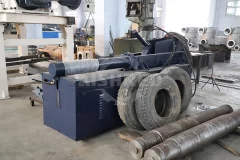
Waste tires contain bead wires, which, if not removed, may cause increased wear and even damage to equipment such as tire shredders. The use of tire debeader can effectively reduce equipment wear and maintenance costs. At the same time, it can greatly improve the efficiency of waste tire processing, reduce environmental pollution, and increase resource recovery rate, making it an important equipment in the waste tire recycling industry, rubber regeneration, and environmental protection industry. The tire debeader, also known as tyre bead wire remover, tire bead wire puller, or bead extraction machine in some regions, is an essential piece of equipment in the waste tire recycling process. As one of the key tire recycling plants in the pre-treatment stage, it efficiently separates the steel bead wires from tires, preparing them for further processing such as shredding, granulation, or pyrolysis.Applicable Tire SizesThe tire debeader is usually suitable for waste tires with a diameter ranging from 800mm to
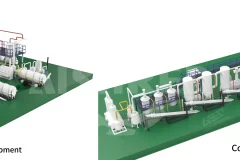
Currently, waste tire pyrolysis and oil refining equipment mainly comes in two types: batch and continuous. When selecting pyrolysis and oil refining equipment, companies often face the dilemma of choosing between batch and continuous equipment. Below, we will compare these two types of equipment in detail from key perspectives such as production efficiency, material requirements, environmental performance, automation level, and cost and return on investment, to help you make a more informed decision. 1. Production Efficiency Batch equipment operates in a batch processing mode, handling a batch of waste tires at a time. After each batch is completed, the equipment needs to be shut down for cooling, discharging products and residues, and then starting the next batch. Although this mode is simple to operate, the frequent start-stop cycles result in shorter effective operating times and lower production efficiency. Continuous equipment, on the other hand, enables 24-hour uninterrupted production. Raw materials
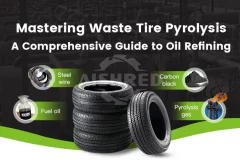
Discover the process of waste tire pyrolysis and oil refining. Learn how thermal cracking transforms tires into valuable resources like tire oil, carbon black, and pyrolysis gas. Explore different technologies, benefits, and applications for sustainable recycling solutions.
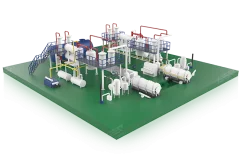
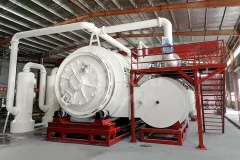
Tire Pyrolysis System
2025-01-13Tire pyrolysis systems offer a comprehensive and high-level recycling solution for end-of-life tires by using high temperatures in a low-oxygen environment to decompose rubber into valuable byproducts such as tire pyrolysis oil, pyrolysis gas, and carbon black. The system typically consists of a reactor (kiln), oil-gas condensation equipment, and a flue gas purification device. Pre-treatment systems may be required in some cases to process tires into suitable sizes.GEP ECOTECH offers two types of tire pyrolysis systems: batch systems and continuous systems. Batch systems are ideal for smaller-scale operations and applications requiring high flexibility, capable of processing whole tires directly. They offer lower initial investment costs and simpler operation. Continuous systems, on the other hand, are designed for large-scale, continuous production, achieving maximum conversion efficiency with pre-treated rubber powder. They offer higher throughput and automation but require a larger initial investment.GEP
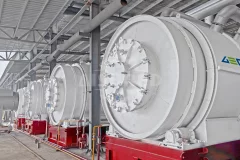
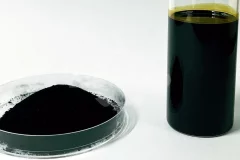
Tire pyrolysis oil refining has become increasingly popular due to its simplicity and high profitability. Many tire recycling companies are adopting or exploring this technology as it not only generates valuable oil from waste tires but also reduces environmental impact. Its flexibility to integrate seamlessly with existing recycling lines makes it an efficient choice for production expansion. Additionally, the process helps lower dependency on fossil fuels by creating alternative energy sources, aligning with global sustainability goals.Price of Tire Pyrolysis Production LineWhen it comes to tire pyrolysis oil refining systems, the cost is a major concern for both newcomers and experienced recyclers. However, the price can vary significantly depending on the system's configuration and capacity. To help you better understand, let’s explore the different types of pyrolysis systems and their general price ranges.Batch-Type Pyrolysis SystemThe batch-type pyrolysis system is the go-to choice for most entry-level
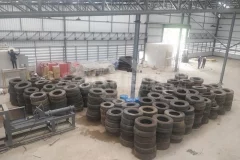
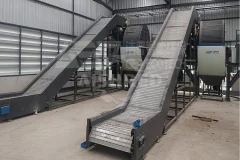
What Would a Tire Granulating Line Be Like?
2024-09-29Recently, a Latin America customer inquired about a 5-ton per hour tire granulation line project, of which 90% are car tires, and the rest are truck tires, tractor tires, bus tires, etc., but the diameter does not exceed 1200mm. The customer's requirements for the discharge particle size are relatively wide, and they have the following applications:1. Around 50x50mm, to be used as a substitute fuel for cement kilns and generates energy through combustion2.<1mm, to be used as rubber powder for fine sand and mortar for construction, or for sewage treatment3. from 2 to 5mm, to be used as a medium: coarse sand for reinforced concrete, paving, and asphalt productionThe client is a turnkey engineering company that provides comprehensive solutions with financial, environmental, and operational goals for various fields such as industry, shopping centers, hospitals, and commercial buildings. After preliminary communication, it has been determined that the project is currently in the feasibility study stage, and our
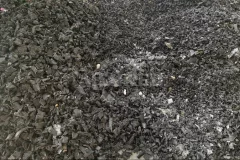
Four-Shaft Shredder for Tyre Crushing
2024-09-10When it comes to shredding tires, there are various equipment options available, such as single-shaft or dual-shaft shredders. However, using GEP ECOTECH's four-shaft shredder offers a significant advantage by shredding tires to a size of less than 40mm in a single pass. Combined with granulators and steel wire separators, this solution can produce clean rubber granules. Get a comprehensive look at GEP ECOTECH's tire recycling solutions
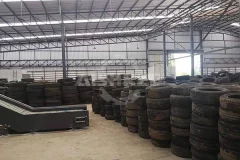
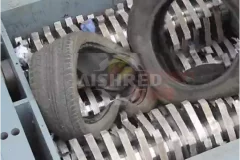
How to Reuse Waste Tires?
2024-03-27There are several ways to reuse waste tires, also known as scrap tires, in an environmentally friendly and economically beneficial manner.Here are some common methods:1. Tire Recycling Plants: These facilities specialize in shredding tires into their original components such as rubber, steel, and fiber. The rubber can be ground into small granulates or powders, which is used in various applications including playground surfaces, athletic tracks, and rubberized asphalt for roads.2. Tire-Derived Fuel (TDF):Tires can be shredded into smaller pieces and used as a fuel source in industries like cement manufacturing and pulp and paper mills. TDF serves as an alternative fuel, reducing the consumption of fossil fuels and diverting tires from landfills.3. Tire Pyrolysis:Pyrolysis is a process that involves heating tires in the absence of oxygen to break them down into oil, gas, and carbon black. The resulting products can be used as fuel, chemical feedstock, or as filler material in various industrial applications.4
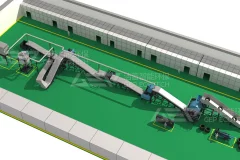
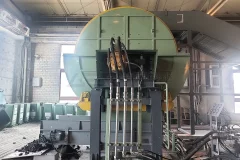
Waste tire recycling machine for rubber powder, also known as rubber powder production line, is designed to convert waste tires into rubber powder or granules for various applications. These machines typically go through several stages to process tires into usable rubber powder. Here are some key components and steps involved in the process:Rubber Powder Production Line1. Tire Shredding:Tire Cutter/Shredder: Used to cut or shred tires into smaller pieces or strips, increasing the surface area for subsequent processing.2. Granulation or Grinding:Rubber Crusher/Grinder: Further reduces the shredded tires into granules or fine rubber powder.3. Magnetic Separation:Magnetic Separator: Removes steel wires and other metallic components from the rubber material obtained from the grinding process.4. Fiber Separation (Optional):Fiber Separator: Separates and removes fiber materials from the rubber powder, depending on the desired purity of the final product.5. Fine Powder Processing (Optional):Fine Grinding/Milling
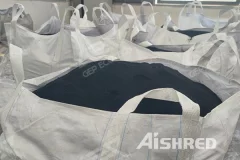
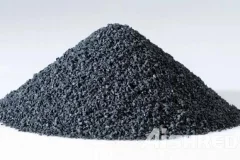
SBR Granules Production Plant
2023-08-01"SBR" is an acronym for "Styrene-Butadiene Rubber," a synthetic rubber known for its versatility and numerous applications. When enhanced with additives, SBR exhibits exceptional resistance to abrasion and aging, making it a preferred choice in various industries. The popularity of SBR granules has grown significantly due to their diverse uses in engineering and construction projects, as well as their wide application in the production of rubber products, road repair, sports surfaces, tracks, rubber flooring, and more. SBR granules are derived from waste tires or other rubber materials through a straightforward and efficient manufacturing process. The key stages of production encompass shredding, steel wire separation, granulation, and fiber separation. GEP ECOTECH boasts extensive expertise in assisting customers with the design, manufacturing, and construction of rubber granule production lines. Our solutions are meticulously tailored to suit specific requirements, including raw materials, site conditions
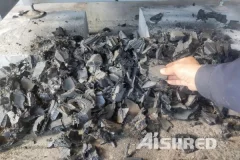
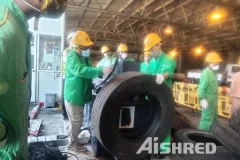
Waste Tyre Recycling Process
2022-05-05Thanks to the development of technology and industry, as well as the standard of living of the population, the number of cars is increasing every year, and with it the production of car tires is also growing. Since their service life does not exceed 5 seasons on average, the problem of the tire recycling process is acute all over the world. Modern tires are a source of valuable materiales and include:Rubber - synthetic or natural, various resins and carbon black, which together form a complex structured rubber shell.Metal elements such as bead rings and reinforcement wire.Textile reinforcement threads made of synthetic fabrics.The remaining components, for example, glue. Due to the development of technology and the improvement of downstream industries, tire recycling has become profitable, and many companies have shown interest in it. Here I‘d like to introduce the process of tire recycling to solve the doubts of many beginners:Scrap Tyres are transported via mechanical trolley into the Processing Warehouse
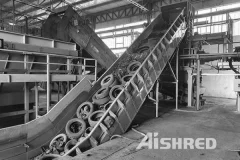
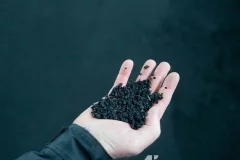
Effective answers to the problem of tire recycling to obtain secondary raw material that can be reused in various fields. Since the beginning of its business, AIShred has been offering careful and effective solutions to the problem of tire recycling, making it possible to obtain - starting from the end-of-life tire - secondary raw material in different grain sizes, with the simultaneous separation of steel and textile fiber.Tires Recycling Processing The first phase of the process involves the extraction of the steel ring present in the tires, which is then stored through different stages of magnetic separation. Subsequently the material is shredded and reduced in size until it reaches a uniform granulometry from 0 to 4 mm. The plant is equipped with a cleaning system articulated in several phases which guarantees the complete separation of the textile fiber, so as to obtain a 99% pure granulated product. Furthermore, an advanced suction system, supported by filters and fire-fighting measures, allows the
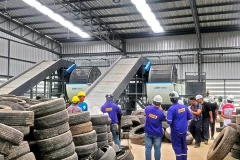
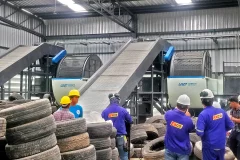
Waste Tire Processing
2022-03-03The management of end-of-life tires has always been an important issue in environmental conservation. Billions of scrap tires are generated globally every year. These accumulated waste not only take up a lot of space but can also cause fires and release harmful chemicals, posing potential threats to the environment and health. Effective recycling of scrap tires is receiving increasing attention. Fortunately, innovative developments are taking place in this area. There are now more mature and environmentally friendly treatment methods for end-of-life tires, which can be converted into derived fuels, recycled rubber, fuel oil, or other useful substances.GEP ECOTECH boasts extensive expertise in tire recycling, offering the capability to design and implement complete production lines tailored to the specific needs. Our versatile range of equipment combinations enables us to meet diverse tire and other rubber products recycling needs—be it recycling rubber chips, granules, powder, or for pyrolysis—at different