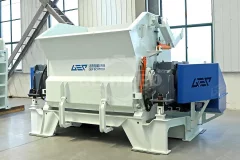
At the beginning of this month, a Southeast Asian customer inquired about wood shredding equipment. The materials to be disposed of are garden waste and wooden pallet scraps, with a processing capacity of 1-3 tons per hour. The feeding size is around 400-500mm, and the discharging size is around 50mm.After preliminary communication with the customer and understanding the basic parameters mentioned above, we confirmed the scope of supply and approximate disposal process with the customer, and then confirmed the product specifications with the engineer. Considering that some nails may be embedded in the scraps of the wooden pallets and need to be collected after shredding, we have added a magnetic separator to the discharge belt conveyor, and this idea has been approved by the customer. Then we sent the proposal and quotation to them.The general process we recommend to the customer is as follows: feeding belt conveyor → European version single shaft fine shredder → discharge belt conveyor → magnetic separator
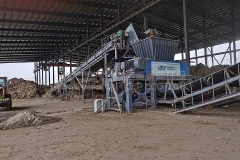
The electricity consumption of a biomass crusher per hour can vary significantly based on various factors, including the machine's specifications, the type of biomass being processed, the machine's efficiency, and the specific operational conditions.GEP biomass crushing project siteThe power consumption of a biomass crusher is primarily influenced by:Machine Type and Specifications: Different models and sizes of biomass crushers have varying power requirements. Taking GEP ECOTECH as an example, our biomass crushers include single-shaft crushers, dual-shaft shear crushers, and four-shaft shear crushers with outputs ranging from 10 to 60 tons per hour. Larger or more powerful machines generally consume more electricity.Biomass Characteristics: Processing different types of biomass materials, such as wood chips, agricultural residues, or forestry waste, may have different densities, moisture contents, and hardness levels, affecting the energy consumption.Crushing Process and Requirements: Crushing biomass to
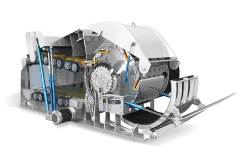
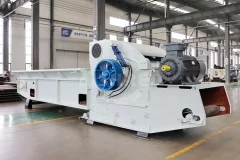
Drum Chipper
2023-08-30Drum chippers utilize a powerful motor to drive the steel drum at high speed, efficiently cutting raw materials into thin slices. By adjusting the operational parameters of the drum chipper, users can flexibly meet the processing needs of different materials, adapting to diverse production scenarios. The drum chipper is suitable for processing various materials, including logs, bamboo, branches, woodworking scraps, medium to high-density fiberboard, pallets, and more.However, drum chippers have a lower tolerance for hard materials such as metal and stone. We recommend separating these materials before processing to reduce equipment wear.GEP ECOTECH's drum chippers feature a horizontal structure with chain plate conveyors, facilitating the feeding of heavy and long materials. Proven in practice, our drum chippers are the ideal choice for efficient wood processing, whether you need them for fuel, biomass briquettes, pulp material, compost additives, or raw materials for recycled wood. Our equipment is designed